Normalize Female Engineers: Using social media to showcase women in engineering can normalize the presence of women in these roles and make them more relatable to young girls.
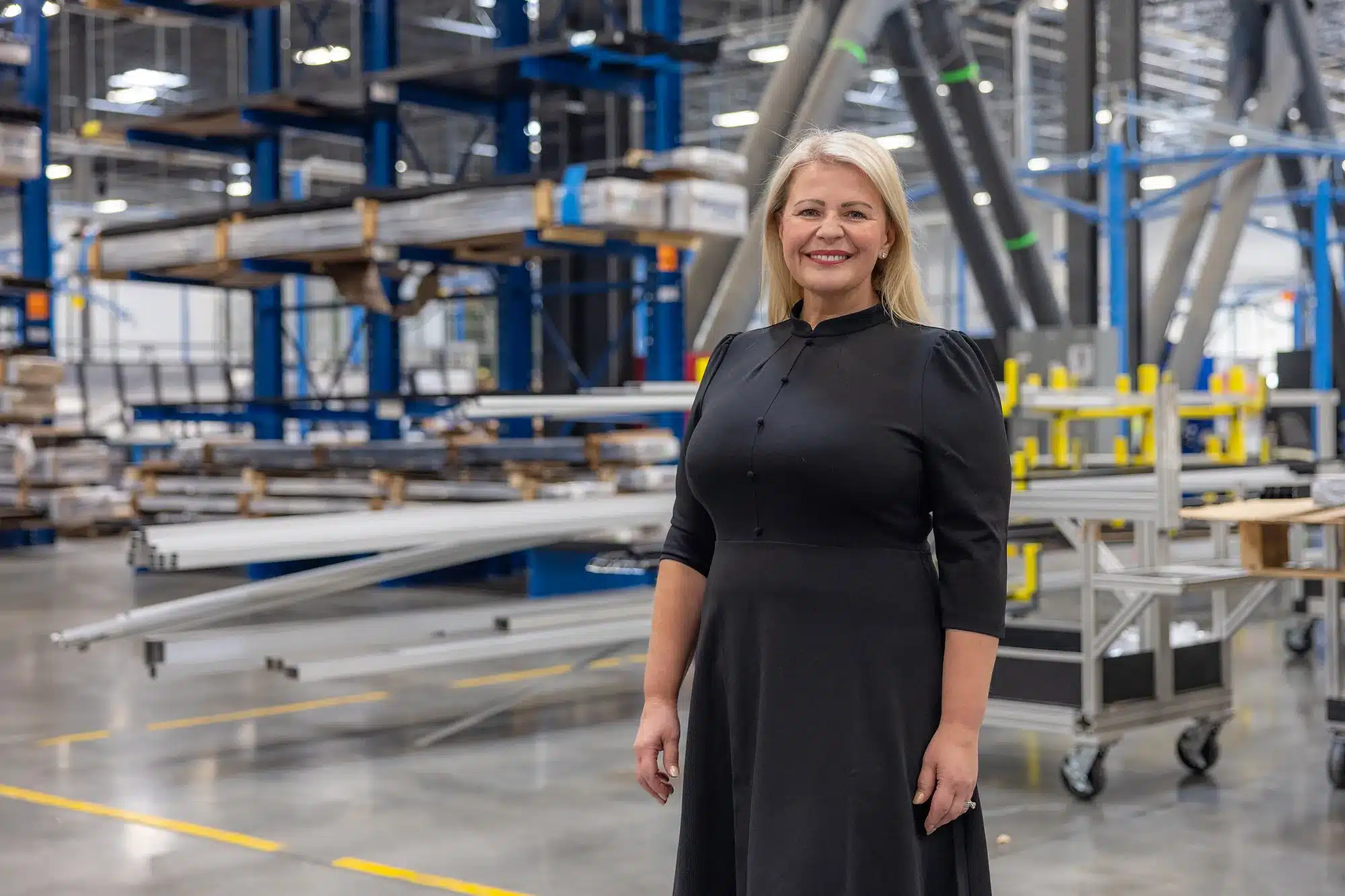
An Interview with Jane Neil by Vanessa Ogle
Originally featured on Medium, this article delves into the gender disparity in STEM and outlines effective ways to boost girls’ engagement in engineering and robotics. Read the full article here: https://www.subzeroeng.com/how-we-can-increase-girls-participation-in-engineering-and-robotics/
Despite the growing importance of engineering and robotics in shaping our future, women remain significantly underrepresented in these fields. This series aims to explore and address the barriers that discourage girls from pursuing careers in engineering and robotics. We are talking to educators, industry leaders, pioneering women engineers, and robotics experts who have made significant contributions to their fields to discuss the strategies they believe can inspire and increase the participation of young girls in engineering and robotics. As part of this series, we had the pleasure of interviewing Jane Neil, Subzero Engineering.
She is a positive self motivated individual with an outgoing personality who offers an analytical view to life and activities. With thirty years experience working in complex and constantly changing environments I have gained well developed organisational, networking, communication and negotiation skills and ability to prioritise and manage extensive workloads.
Through the unique experience of life and rigour within the Royal Navy, high pressure, time bound commitments on self and team was commonplace, this provided extensive travel and extended experience of numerous cultures.
Strong technical background with practice in Engineering, Quality, Manufacturing and Supply Chain gained in heavy engineering within construction, pump equipment and automotive industry. Working knowledge of numerous quality systems and standards both from a compliance and an implementation perspective.
Her recent Supply Chain experiences have developed the ability to understand explicit and implicit customer needs while building internal and external working relationships across global regions. This has also developed Project Management competence, involving multiple stakeholders with varying needs, using influencing skills in a variety of customer and supplier situations, delivering results through people. All aspects of people management from recruitment to performance, an ability to identify support and development needs within teams.
Thank you so much for doing this with us! Before we dig in, our readers would like to get to know you a bit more. Can you tell us a bit about your “backstory”? What led you to this particular career path?
I’ve always been drawn to engineering, It’s very much an internal feeling. But it was out of necessity as my parents separated when I was very young, so if anything broke in the house, I was the one who wanted to fix it so my mum wouldn’t worry. I would carry out many simple manual tasks, such as plastering walls or laying bathroom tiles. I remember once the washing machine broke, and I gave my mum an electric shock in my attempts to fix it!
Back then, around 35 years ago, it was rare to find females in engineering roles. Luckily for me, the British Royal Navy changed that, and for the first time in history women could go to sea. That also meant that females could be engineers. Before then, the stereotypical WREN was handbag and court shoes, all very British.
I’ve been around the world, and I’ve done a lot. Since the Royal Navy I’ve been in many different manufacturing and engineering environments, from marine engineering, automotive, and pump manufacturing. The oil, gas and nuclear industries were prominent in my earlier career path and that’s before I went into more high-tech electronics.
Can you share the most interesting story that happened to you since you began your career?
When I first started, the uniform issued to me was a mix of both male and female designs, because I was only the seventh woman to go to sea as an engineer. We were pioneers, not entirely sure what to expect. My first military assignment was during the Bosnia War, where I was awarded a NATO medal for peacekeeping. That was in my first three months at sea!
What inspired you to pursue a career in engineering or robotics, and how can we replicate that inspiration for young girls?
The UK Government presented the opportunity to me, but for future generations, targeted marketing and social media can be powerful tools. How can you get a female’s attention when you are competing with fashion and diet pills on Instagram, etc? Highlighting the potential for high salaries in electronics and engineering could be appealing.
We need to educate young people in digestible chunks while they’re still in that sweet spot of discovery and understanding, to show them what the future could look like! There are so many different elements to engineering and, for many, it can be quite overwhelming. Social media can play a big role in making these concepts accessible and normalizing the idea of women in engineering.
It’s also interviews such as these, where you can see that I have a normal life, kids and family, my work-life balance in check, I have a management role, and this is the salary bracket. Being here, proving to people that I’m doing the job, demonstrates to younger females that women are in management and engineering roles now, that we are supportive of those young girls coming in.
The path forward is now carved out, though it’s still narrow. When I was younger, the route wasn’t smooth — you had to climb rocks, overcome obstacles, and break through barriers. But today, that path exists.
I encourage women to walk that path, knowing there are others ready to support them along the way. As managers in engineering environments, it’s our responsibility to recognize and nurture the talent in the young.
There is a duty of care, a real sense of responsibility to guide the talent in the young females and give them stretch assignments. I’m always challenging the females in the work environment to be uncomfortable. Because being uncomfortable is good. It may not feel that way, but you must move your thinking because you only ever grow when you’re out of your comfort zone. Uncomfortableness equals growth and you will have no idea what you can achieve if you don’t learn to see it positively!
None of us are able to achieve success without some help along the way. Is there a particular person who you are grateful towards who helped get you to where you are? Can you share a story about that?
My sense of responsibility stems from the fact that I didn’t really have any work mentors or significant figures guiding me through my career. While I never felt recognized for my struggles, it taught me the importance of recognizing and nurturing talent in others. People nowadays are so concerned with themselves that they don’t have the time, space, or energy to recognize other’s talents, but that doesn’t mean that you’re less talented.
The adversity that I went through helped make me the person and the leader that I am today. It possibly makes me fiercer and more courageous. My career path may not have been a smooth ride, but that’s not real life, is it?
Is there a particular book that made a significant impact on you? Can you share a story or explain why it resonated with you so much?
A coach called David Allen, and his program called Getting Things Done (GTD) made a significant impact on me. I got hold of an audio file of a seminar that he did probably 15 years ago, and I just loved it. It’s about time management & high performance. I still listen to the audio file today if I get bogged down or too busy. I’ll just play one of them and it lifts me up to where my thinking needs to be. It taught me how to mind map and how not to worry about the things I wasn’t doing so I had the energy to focus on the highest value projects. And it taught me how to extract those blockages from my brain, whether via high tech or low tech so that it wasn’t jamming my creativity.
As females we often worry about what we’re not doing, and don’t celebrate what we are doing well. Changing that mindset has made me a better mother, wife, employee, manager, everything. One of the most valuable pieces of advice I ever received came from the GTDs. I use it with my team: when we are naturally good at something, we often take that magic and put it in a zero-value bucket because we think it’s natural and therefore not special. We need to take our natural talents back out of the zero-value bucket as it’s our super power!
Do you have a favorite “Life Lesson Quote”? Do you have a story about how that was relevant in your life or your work?
My favorite life lesson quote is from a Jack Canfield book. It’s ‘no blaming, no complaining, no excuses’. It leaves you nowhere to go, so you’re forced to own it. I was always taught by my mother to look in before you look out. We live in a world today where we’re so easily distracted with information bombarding us from all angles, that we’re constantly looking to the next answer and not concentrating on what we have in front of us. I believe the answers are always inside us. We just need to find the peace and quiet inside and take a minute to listen.
I use this life lesson quote in my day-to-day work and ask my team to do the same. Once you take the blame or complain out of the equation it becomes easier to look at the challenge and deal with it head on.
According to this report, only about 16% of engineering positions in the US are held by women. This reflects great historical progress, but it also shows that more work still has to be done to empower women. In your opinion and experience what is currently holding back women from Engineering and Robotics?
As females, we can sometimes gravitate to areas and environments where there are more women around, sub-consciously avoiding those that are more male-centric. Women might have an idea of what a normal day looks like if they work in, for example, marketing, which is perhaps a more balanced role, but I don’t think we’re quite there yet on the engineering front. Again, social media can help in demystifying roles, and showing what a normal day in an engineering role is like. In addition, the availability of more equal salaries in this industry helps women to know that they are valued more equally.
This might be intuitive to you but I think it will be helpful to spell this out. Can you share a few reasons why more women should enter the Engineering and Robotics fields?
Women are natural problem solvers. We look at things in a different perspective from men. Our brains are wired differently, so we can look at a challenge from all the different angles, which in turn offers more innovation. It’s a beautiful thing for a female to bring to engineering environments and there is huge satisfaction that comes from problem-solving, improving things, and innovating. Your self-esteem, your happiness, your take on life, the confidence that grows; you don’t have to think or feel like a man to bring that talent into the workplace. Diversity leads to greater innovation, and having more women in engineering will only accelerate progress.
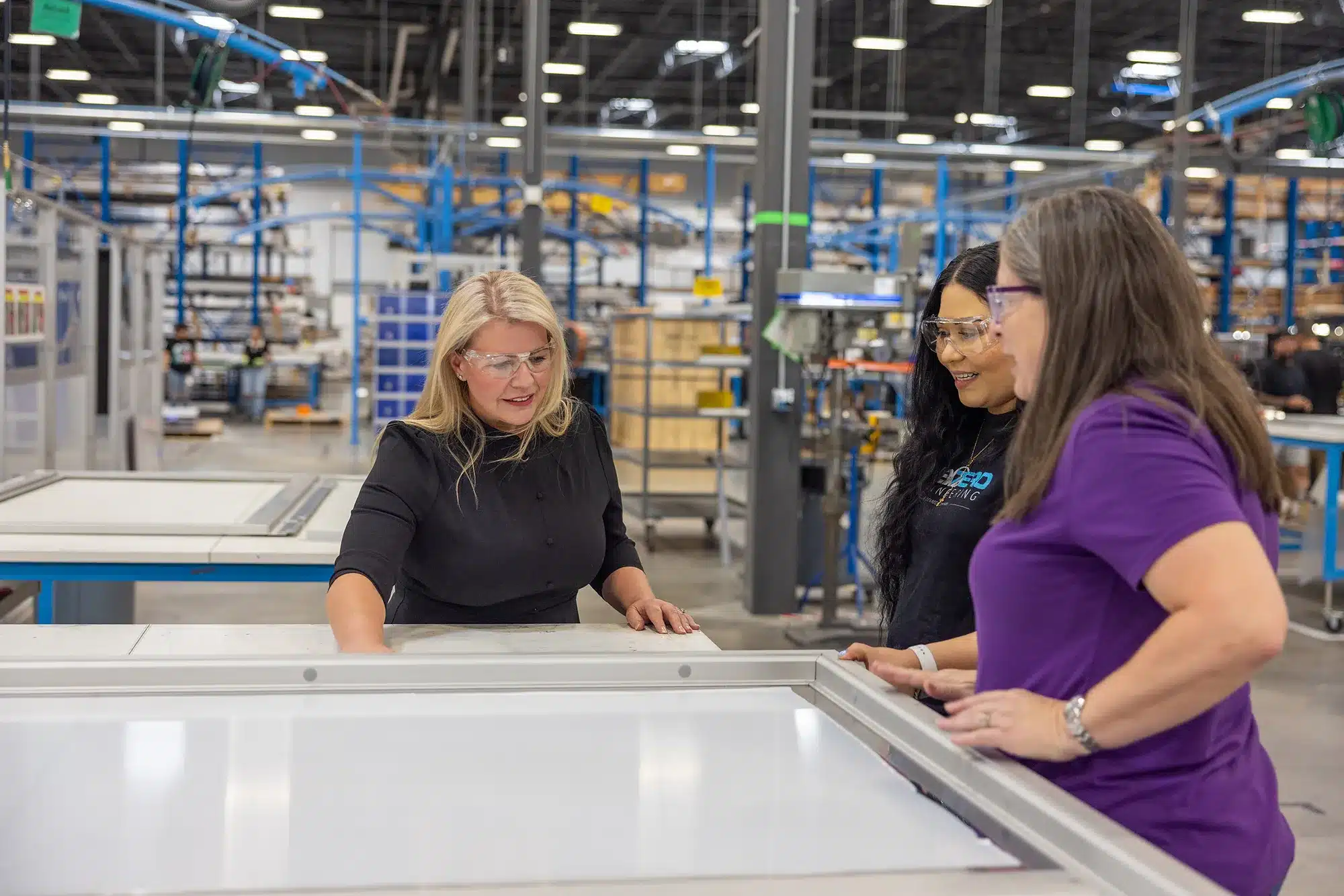
Can you please share “5 Things We Need To Increase Girls’ Participation in Engineering and Robotics?”
1. Role Models in Schools: While STEM stuff is prominent in schools right now, it’s doesn’t quite translate into jobs available for females in engineering. Middle school is a critical time for kids to discover potential career paths. Having female engineers speak at schools and share their experiences can help demystify the field and inspire young girls.
2. Clear Educational Pathways: Highlighting courses available in college and how they translate into a career for women, would be a big improvement. If I’d had that knowledge at that age, my path would have been a much easier one to take.
3. Educate in Bite-sized Chunks: Educating young people to show them what their potential can look like. If we introduce young girls to the many different elements of engineering and the many different industries that engineering is a part of, rather than just a high overview, would really help the next generation to understand the innovation and change aspect. All too many times, people just don’t understand what we do, so to break down the many various elements of it in bite-size chunks of learning would help.
4. Normalize Female Engineers: Using social media to showcase women in engineering can normalize the presence of women in these roles and make them more relatable to young girls.
5. Promote Salary Parity: Demonstrating to young people that they can earn the same salaries as their equal male counterparts is powerful. Women deserve equal parity and pay, and that was part of the attraction for me when I was younger. I don’t think we’re fully there yet, but we are moving in the right direction.
In your opinion, what are the most effective ways to introduce girls to engineering and robotics at an early age?
It would be helpful if school visits with groups of females who had shown an interest in engineering could come into the company, how often do you see the inside of an organization at that age? Introducing young people to what the manufacturing environment looks like, how it feels to be in the building and meeting the people that work there would be very effective. If local businesses could be attached to school programs, and have classes come and physically walk around the business — it could be enough to spark a light.
Educational programs at the school level, hands-on learning experiences and opportunities, and fostering inclusive and supportive environments would encourage young women into the industry. A lot of impressionable young women worry that the industry is too male dominated and that can feel quite intimidating. Seeing real women who actually work in the industry and talking with them about day-to-day life would put a lot of young women at ease.
30% of office and 25% of production are female, we are a super supportive bunch! We want the absolute best for each other, it’s a magical environment. We would love to show our next female generation just how supportive we can be.
How do you think the portrayal of women in STEM fields by media and educational materials impacts girls’ interest in engineering and robotics?
Social media can impact girls’ interests, but I don’t think there is enough positive content to be found on the platforms, or that it’s real enough. It’s still very much at a high overview perspective, and it needs to be broken down into much more real-life examples for young people to be able to digest and absorb. Our marketing video has many women in production, and it does a great job in showing the reality of the industry. We need more displays of females in their normal place of work.
What advice would you give to girls who are interested in engineering and robotics but are hesitant to take the first step?
The path has been carved now, and, as females, we should be stepping onto it. The more that we do, the wider the path will become and the smoother the journey. We are always building our way for the future of females, so we’re not only responsible for ourselves, but we’re also responsible for whoever is coming next. We don’t have to be masculine anymore. We can make a real difference in engineering, and that is very, very satisfying. It’s a role where you can look back and say, I made a change. That could be a change in technology or an office environment for other females. Feminism has evolved; it is about heart, soul and humility. Bringing your diversity to an engineering environment where you are involved in the change for the future is a nourishing and rewarding place to be.
You are a person of great influence. If you could inspire a movement that would bring the most amount of good for the greatest number of people, what would that be? You never know what your idea can trigger.
“Women in Clean Tech” is the movement I’d inspire!
Women Engineering a Sustainable Future. It combines two crucial elements: increasing diversity in engineering and addressing environmental challenges. This movement would promote mentorship programs, collaborative eco-tech projects, and sustainability-focused innovations.
By encouraging more women to enter engineering fields, we can tap into a wealth of undiscovered potential. This diversity brings fresh ideas and approaches to problem-solving, which is crucial when tackling complex issues like climate change and resource scarcity. Utilizing individual talents to strengthen a group, recognizing and leveraging the unique skills and perspectives that each member brings to the table.
I recently implemented a recyclables project, led by a female on my team is a small example of this potential. Imagine this amplified globally — women engineers spearheading a more sustainable world. By merging gender diversity with environmental action, we can create positive change that benefits everyone and creates a powerful synergy.
Thank you for these fantastic insights. We greatly appreciate the time you spent on this.
About The Interviewer: Vanessa Ogle is a mom, entrepreneur, inventor, writer, and singer/songwriter. Vanessa’s talent in building world-class leadership teams focused on diversity, a culture of service, and innovation through inclusion allowed her to be one of the most acclaimed Latina CEO’s in the last 30 years. She collaborated with the world’s leading technology and content companies such as Netflix, Amazon, HBO, and Broadcom to bring innovative solutions to travelers and hotels around the world. Vanessa is the lead inventor on 120+ U.S. Patents. Accolades include: FAST 100, Entrepreneur 360 Best Companies, Inc. 500 and then another six times on the Inc. 5000. Vanessa was personally honored with Inc. 100 Female Founder’s Award, Ernst and Young’s Entrepreneur of the Year Award, and Enterprising Women of the Year among others. Vanessa now spends her time sharing stories to inspire and give hope through articles, speaking engagements and music. In her spare time she writes and plays music in the Amazon best selling new band HigherHill, teaches surfing clinics, trains dogs, and cheers on her children.